views
Applications of Incoloy 825 Instrumentation Fittings in the Oil & Gas Industry
With molybdenum, copper, and titanium added, Incoloy 825 is an extremely corrosion-resistant alloy made mostly of nickel, iron, and chromium. The oil and gas industry favors it because of its remarkable resistance to a variety of corrosive situations. Instrumentation fittings, which are crucial parts used to connect, operate, and monitor fluid and gas systems, are among its most significant applications.
1. Corrosion Resistance in Harsh Environments
Subsea operations and sour gas fields are two examples of highly corrosive settings where oil and gas production and processing frequently occur. In both oxidizing and reducing situations, Incoloy 825 instrumentation fittings provide exceptional resistance to stress corrosion cracking, pitting, crevice corrosion, and general corrosion caused by chloride. Because of this, they are perfect for usage in refineries, downhole equipment, and offshore rigs.
2. High-Temperature Applications
At higher temperatures, Incoloy 825 retains its corrosion resistance and mechanical strength. In the oil and gas sector, high-pressure and high-temperature (HPHT) operating conditions are common for instrumentation systems. Heat exchangers, separators, and pressure vessels where dependable operation under heat stress is essential employ Incoloy 825 fittings.
3. Chemical Injection and Control Systems
Corrosion inhibitors, demulsifiers, and other treatment chemicals are injected into production wells and pipelines using chemical injection systems. Because these chemicals are harsh, the fittings utilized in these systems need to be able to withstand their effects. Because of its exceptional resistance to a range of acids, including sulfuric, phosphoric, nitric, and organic acids, Incoloy 825 instrumentation fittings are frequently utilized in these kinds of applications.
4. Subsea and Downhole Equipment
Materials that can tolerate high salinity and pressure are necessary for submerged oil exploration. Because of its strength and resistance to corrosion, Incoloy 825 can be utilized for subsea instrumentation fittings in chemical injection modules, hydraulic lines, and control systems. Additionally, it works well in downhole tools, where parts are subjected to corrosive brines, high temperatures, and pressures.
5. Gas Processing and Transportation
Water vapor, carbon dioxide, and hydrogen sulfide (H2S) are among the impurities that must be eliminated during the processing of natural gas. Standard materials may corrode severely as a result of these pollutants. Particularly in sour gas service where hydrogen sulfide levels are high, Incoloy 825 instrumentation fittings guarantee system dependability and safety during gas treatment and transportation.
6. Safety and Reliability
Fittings for instruments are essential for tracking temperature, flow, and pressure. When these parts fail, there may be safety hazards and expensive downtime. Because of its exceptional durability, leak-proof connections, and long-term dependability—even in harsh media and variable conditions—Incoloy 825 provides peace of mind.
Conclusion
Because they are long-lasting, resistant to corrosion, and perform well in demanding operating conditions, Incoloy 825 instrumentation fittings are essential to the oil and gas sector. Their application in vital systems, such as gas processing facilities and offshore platforms, contributes to operational longevity, safety, and efficiency. Purchasing premium fittings made of Incoloy 825 can improve the overall integrity of vital infrastructure in this demanding industry and drastically lower maintenance costs.
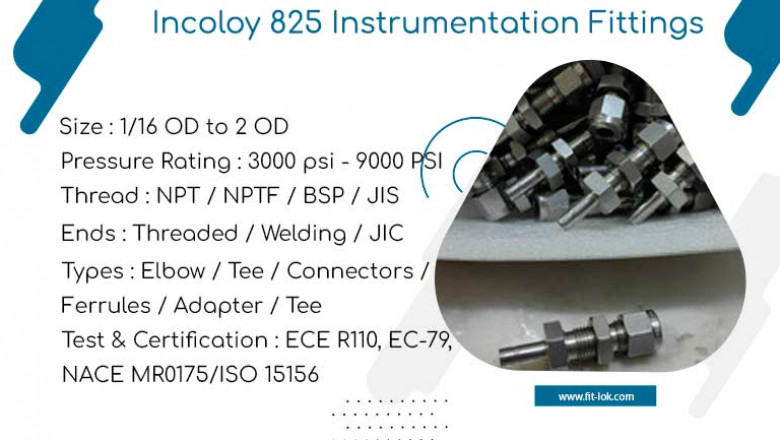

Comments
0 comment