views
As businesses operate under tighter timelines and higher expectations, effective work order management becomes a cornerstone of operational success. Whether in facility services, production environments, or IT support, having a structured system to assign and complete tasks is essential. This guide walks through the building blocks, advantages, strategies, and decision-making elements of work order management, while weaving in vital keywords for digital discoverability.
Work order management is the method of organizing and executing the assignments necessary to maintain smooth operations. From routine tasks to unplanned repairs, having a clear and consistent approach ensures better performance and reliable service. With tech-driven solutions now mainstream, organizations can cut down on manual processes, avoid errors, and enhance visibility across all functions.
Work orders are the engine of your maintenance operation. They power your team and move work from point A to point B. Work order management is crucial to an organization's operation, Visit at @ https://toolkitx.com/campaign/workorder-management/
Why Work Order Management is Essential
Efficient work order management is essential for businesses aiming to optimize operational workflow and reduce downtime. Here are some of the reasons why organizations invest in this critical process:
- Improved Operational Efficiency: With an automated work order tracking system, companies can assign, monitor, and update tasks in real time. This ensures that all work is addressed promptly and resources are allocated efficiently.
- Cost Reduction: By implementing preventive maintenance and streamlining job scheduling, organizations can avoid costly emergency repairs and extend the life of critical assets.
- Enhanced Communication: Modern systems enable clear communication between teams. With mobile and cloud‑based solutions, field technicians and managers can access work orders anytime and anywhere.
- Data‑Driven Insights: Detailed reporting features help management identify bottlenecks, forecast maintenance needs, and make informed decisions based on historical data.
Key Components of a Work Order Management System
Understanding the key components of a work order management system is crucial in selecting the right solution and optimizing your operations. These systems are designed to cover the entire lifecycle of a work order—from creation and scheduling to resolution and reporting.
1. Work Order Creation and Scheduling
The first step in the process is the creation of a work order. Modern systems allow users to quickly generate digital work orders using standardized forms. They can capture essential details such as the task description, location, priority level, and required materials. Scheduling tools then help assign the right technician or team to the job based on availability and expertise.
2. Assignment and Dispatch
Once the work order is created, it is vital to assign it to the appropriate personnel. A key aspect of effective workflow automation is the ability to dispatch tasks automatically based on predefined criteria. This minimizes delays and ensures that each task is handled by someone equipped to resolve it.
3. Execution and Mobile Integration
A major advantage of modern work order management systems is mobile integration. Field technicians can receive notifications directly on their smartphones or tablets, allowing them to access the details of the job on the go, capture real-time images, update status, and even communicate with dispatchers. This level of mobility significantly enhances the responsiveness and accountability of the maintenance team.
4. Completion and Reporting
After a work order is completed, it is critical to document the service performed. Detailed notes, photos, and other evidence of task completion can be recorded in the system for future reference. Comprehensive reporting not only assists in compliance but also offers valuable insights into operational efficiency and potential areas for improvement.
Best Practices in Work Order Management
Implementing an effective work order management strategy requires more than just adopting the latest technology. It involves organizational change, clear communication, and continual process refinement. Consider the following best practices:
Standardize Processes
Develop standard operating procedures (SOPs) to ensure that each work order is consistently handled. Use detailed templates for work orders to capture all necessary information, reducing the likelihood of errors.
Leverage Automation
Invest in work order management software that offers advanced automation features. Automation can minimize manual data entry and ensure that tasks are assigned based on current resource availability and priority levels.
Integrate Systems
An integrated approach is essential. Work order management should not exist in isolation but should be part of a broader maintenance management or enterprise resource planning (ERP) system. This allows seamless data sharing across departments, enhancing overall business intelligence.
Embrace Mobile Technology
Make the most of mobile capabilities to ensure your workforce is connected at all times. Mobile integration not only improves responsiveness but also captures real‑time data that can drive future process improvements.
Continuous Improvement
Regularly review and analyze work order management data to identify trends, areas for improvement, and training opportunities. By continuously refining your processes, you can ensure that your system adapts to evolving business needs.
How to Choose the Right Work Order Management Software
Selecting the right work order management system involves aligning the capabilities of the software with your business needs. When evaluating options, consider the following factors:
Usability and Customization
Look for software that is user-friendly and can be customized to fit your specific industry requirements. The ideal system should integrate seamlessly with existing technologies and easily adapt to changes in your workflow.
Scalability
Your business may grow, and your software should grow with it. Ensure that the system you choose can handle increasing volumes of work orders and expanding teams without sacrificing performance.
Reporting and Analytics
Robust reporting and analytics features are essential for uncovering hidden inefficiencies. The system should provide customizable dashboards and in‑depth reports that help you understand the dynamics of your work order flow.
Customer Support
Technology is only as good as the support behind it. Choose a vendor that offers reliable customer support, training resources, and a clear roadmap for future upgrades.
The Future of Work Order Management
As industries continue to digitize their operations, the future of work order management is likely to be shaped by advancements in artificial intelligence (AI) and the Internet of Things (IoT). These technologies promise even greater automation, predictive maintenance, and integration capabilities. By embracing these innovations, businesses can enhance operational efficiency, reduce downtime, and improve overall service quality.
Work order management remains a cornerstone of operational excellence in a wide array of industries. By implementing effective work order management strategies and leveraging modern work order software, organizations can achieve significant efficiency gains, reduce costs, and improve customer satisfaction. As technology continues to evolve, adopting an integrated, mobile‑first, and data‑driven approach will become essential for staying ahead in today’s competitive business landscape.
Frequently Asked Questions (FAQs)
1. What is work order management?
Work order management is the process of creating, tracking, assigning, and completing tasks or jobs required for maintenance, repairs, or service requests. It ensures that work is efficiently distributed and completed, reducing downtime and increasing productivity.
2. How does work order management software help streamline operations?
Work order management software automates the creation, dispatch, and tracking of work orders. It enables real-time updates, integrates mobile technology for field operations, and provides detailed reporting and analytics, all of which contribute to enhanced operational efficiency.
3. What are the essential features to look for in a work order management system?
Key features include work order creation and scheduling, mobile integration, real-time status updates, automated dispatch, customizable reporting, and seamless integration with other systems such as ERP or maintenance management systems.
4. Can work order management reduce operational costs?
Yes, by automating processes, scheduling preventive maintenance, and reducing emergency repairs, work order management can significantly lower operational costs. The system also helps optimize resource allocation, reducing labor and material wastage.
5. How does work order management integrate with other business systems?
Modern work order management systems are designed to integrate with various business tools such as ERP software, Customer Relationship Management (CRM) systems, and Computerized Maintenance Management Systems (CMMS). This integration facilitates seamless information flow, ensuring that all parts of the organization work in sync.
Browse More Articles
https://saastoolsblog.blogspot.com/2025/04/optimizing-work-order-management-for.html
https://sites.google.com/view/efficient-work-order-managemen/home
https://newdoorfiji.com/streamlined-work-order-processes-for-enhanced-flow/
https://pdf24x7.com/live/revolutionizing-work-orders-for-operational-success
https://postyourarticle.com/modernizing-work-order-systems-to-maximize-productivity/
https://linkgeanie.com/news/enhancing-operations-with-smart-work-order-management-system
https://edutous.com/seamless-work-order-management-for-operational-excellence/
https://posteezy.com/optimized-order-management-driving-operational-flow
https://bdnews55.com/2025/04/15/transforming-work-orders-for-agile-efficient-operations/
https://www.bloglovin.com/@aaronmyres/next-gen-work-order-systems-empowering-operational-13437591
http://toolkitxsaasblog.weebly.com/blogs/digital-work-order-management-for-a-modern-operational-era
https://livepositively.com/empowering-your-business-with-effective-work-order-systems/
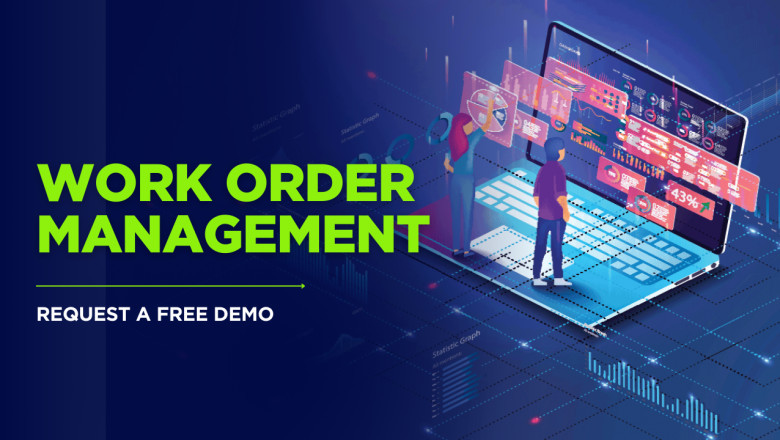

Comments
0 comment